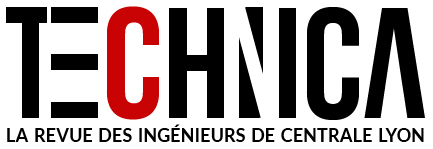
Retour au dossier
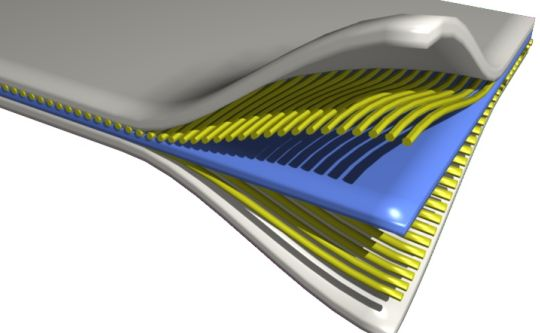
Vue 886 fois
09 décembre 2019
Les matériaux composites à fibres discontinues et leurs avantages
LES MATÉRIAUX COMPOSITES sont constitués de plusieurs matériaux non-miscibles aux propriétés complémentaires. Cette combinaison permet en général de produire des matériaux qui disposent de propriétés qu’aucun des composants initiaux ne possède. Un matériau composite est en générale composé d’inclusions rigide (e.g. fibres…) enveloppées dans une matrice plus ductile (e.g. résine, polymère). Le concept existe depuis longtemps avec, par exemple, les cabanes en paille et terre séchée, mais même bien...
Cet article est réservé aux membres cotisants
Aucun commentaire
Vous devez être connecté pour laisser un commentaire. Connectez-vous.