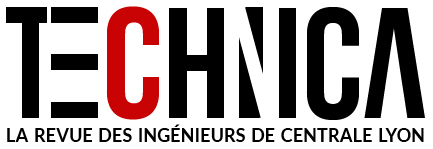
Retour au dossier

Image annca de Pixabay
Vue 548 fois
09 décembre 2019
De nouveaux matériaux pour l'aéronautique
La traque des kilogrammes !
L’industrie aéronautique a toujours été en quête de matériaux innovants afin de réduire la masse des machines volantes. C’est d’autant plus vrai aujourd’hui, avec le développement accéléré des véhicules électriques/ hybrides. Chaque kilogramme économisé permet de parcourir davantage de distance avec la même énergie. Autrement dit, c’est aussi moins de kérosène, et donc moins de CO2 produit, pour le même vol. Sachant que le carburant représente environ 30 % des coûts d’exploitation d’une...
Cet article est réservé aux membres cotisants
Aucun commentaire
Vous devez être connecté pour laisser un commentaire. Connectez-vous.