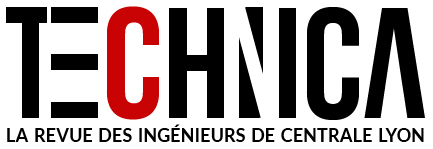
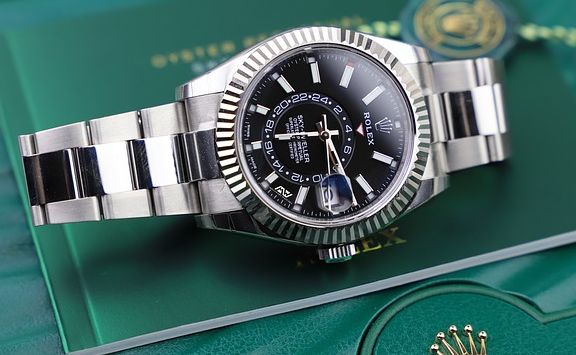
Rencontre avec deux ingénieurs ECL du service R&D de Rolex SA
A l’heure où le temps semble s’être arrêté en raison de la crise du coronavirus, nous sommes partis à la rencontre (virtuelle) d’Élodie Grosset et Julien Caillol, tous deux issus de la promo 2005 de Centrale de Lyon, qui travaillent comme ingénieurs chez Rolex SA. Ils nous parlent avec passion de leur métier, de la façon dont il a évolué ces dernières années, et de la diversité des projets dont ils ont la responsabilité.
Bonjour Élodie et bonjour Julien. Pouvez-vous nous présenter vos postes respectifs chez Rolex ?
Élodie Grosset : Je travaille à Genève chez Rolex SA depuis 2005, en tant que chargée de projet Fiabilité au sein de la division R&D. Ma principale mission est de valider que les nouveaux calibres (mécanismes à l'intérieur de la montre) qui sortent soient fiables, c'est-à-dire qu’ils répondent aux exigences demandées en termes de performances à neuf et dans le temps. Je n'ai pas de responsabilité hiérarchique directe, mais un rôle d'expertise. Nous travaillons beaucoup en mode projet avec des équipes pluridisciplinaires. Il y a aussi un aspect méthodologie dans mon métier, avec par exemple des réflexions sur les moyens de tests ou les méthodes d'analyse (statistiques, exploitation du retour d'expérience, etc).
Julien Caillol : Quant à moi, je travaille également à Genève chez Rolex SA mais depuis 2006. Je suis chargé de projet Construction au sein de la division R&D. Je participe à la conception et au développement des bracelets et des boites des nouveaux modèles de montres (contrairement à Élodie, je ne travaille pas sur les mécanismes). Mes missions sont les suivantes :
- Développement (Dimensionnement, tolérancement, ...) des nouveaux produits en lien avec les designers et les services d'industrialisation
- Recherche de nouveaux concepts pour les futures montres
- Méthodologie de travail : PLM, Outils CAO, Cotation, Veille technologique
Élodie, peux-tu nous expliquer les différents process qui permettent de vérifier les nouveaux calibres d'une montre ? Quels sont les principales difficultés à surmonter (techniquement) pour garantir leur fiabilité ?
On doit vérifier la précision chronométrique, c’est-à-dire si la montre avance ou retarde, et ce dans différentes situations. On regarde par exemple l’impact de chocs, de chutes, du magnétisme, d’une surpression d’eau en condition de plongée, de la température, etc.
On doit aussi garantir la fiabilité dans le temps des calibres. Pour cela, il nous faut d’abord réfléchir à ce que ferait un client avec sa montre (par exemple : combien de fois par année va-t-il régler l’heure et la date de sa montre ? Comment se sert-il de sa fonction chronographe ?).
Il faut ensuite réussir à reproduire la sollicitation sur des moyens d’essai, pour simuler un certain nombre d’années de porter de la montre. On mesure souvent en continu certaines grandeurs au cours du vieillissement afin de suivre l’évolution du système dans le temps (on va par exemple suivre un couple en faisant des cycles d’armage et désarmage d’un ressort).
On veut non seulement que les systèmes ne cassent pas, mais aussi que les sensations pour le client restent agréables. On peut tester des éléments seuls (fiabilité d’un ressort par exemple), ou bien seulement un système (par exemple la fonction mise à l’heure) ou encore le mouvement entier.
Les principales difficultés techniques viennent d’abord des dimensions des pièces, qui sont très petites. Les moyens de test et de mesure doivent donc être très précis.
De plus, reproduire au plus juste la gestuelle humaine, quand par exemple on active une fonction en appuyant sur un poussoir, est souvent difficile : vitesse de déplacement, pression de contact, amortissement…
Enfin, il y a de nombreux points de lubrification dans un mouvement. Il est difficile de simuler correctement leur vieillissement dans le temps, et pourtant c’est souvent le manque de lubrifiant, son déplacement hors du contact ou sa modification physico-chimique qui vont créer de l’usure et donc une altération de la fonction.
Julien, tu parlais de "Développement (Dimensionnement, tolérancement, ...) des nouveaux produits". Peux-tu nous expliquer de quoi il s’agît ?
C’est le fait de passer d’un concept ou d’un prototype unique qui a servi de démonstrateur esthétique ou technique à un produit qui est industrialisable, et qui répond aux performances attendues. Lorsqu’on fait un démonstrateur, toutes les techniques de fabrication sont possibles, le coût et le temps de fabrication n’ont pas d’importance. Ensuite il faut s’adapter aux process des ateliers de fabrication, faire attention aux coûts, respecter les normes, les engagements de la marque, utiliser les bons matériaux et prendre en compte les problématiques de contrôle. Par exemple on peut réaliser un prototype en laiton facile à usiner et le flasher en or pour obtenir un rendu esthétique permettant de le valider, mais une telle pièce ne peut pas être vendue. Il faut ensuite revoir le mode de fabrication pour l’adapter à la matière définitive.
Il faut aussi s’assurer que tous les produits vendus respecteront les performances annoncées au client en tenant compte des dispersions de fabrication de chacun des composants. Le dimensionnement consiste par exemple à s’assurer que la montre résistera à certains chocs, qu’elle ne se déformera pas sous l’effet de la pression, si on prend la Deepsea qui est garantie étanche à 3900m, les efforts que subit la boite sont colossaux. Autre exemple, sur un poussoir qui actionne un chronographe, on s’assure que l’effort du ressort est le même dans toutes les montres et qu’il ne va pas varier dans le temps.
Il faut aussi garantir le montage des pièces entre elles et leur interchangeabilité pour le SAV.
Reprenons un peu de recul. Quels ont été vos parcours à tous les deux avant de rejoindre Rolex ?
Élodie : J’avais pris l’option Matériaux et Technologies en 3A à Centrale. Tout ce qui touche à la tribologie me plaisait particulièrement et Rolex a proposé au LTDS un Travail de fin d’études sur la Tribologie du Platine. J’ai été embauchée suite à cela pour terminer le travail commencé lors du stage.
Julien : Je souhaitais faire l’option Génie Industriel Conception en 3A, il y avait beaucoup de demandes cette année-là et je n’avais pas été retenu. J’ai donc fait une année de césure chez CESA, une PME à Feysin qui concevait, assemblait et installait des systèmes de convoyage et de tri dans des ateliers de fabrication comme la chocolaterie Révillon ou des centres de tri de La Poste par exemple. On travaillait en petite équipe : un technicien-commercial, deux ou trois monteurs, un technicien mécanique (mon rôle) et un technicien informatique. Je m’occupais de la conception, la maîtrise d’œuvre pour le montage et la mise en service des systèmes ainsi que de la relation technique avec les fournisseurs. Cette année, qui était plus qu’un stage puisque j’étais considéré comme un employé à part entière de l’entreprise, m’a conforté dans l’idée de poursuivre dans la conception mécanique.
J’ai donc fait ma 3A en Génie Industriel Conception et à l’époque il y avait un bon partenariat avec Rolex pour les stages, notamment en conception par l’intermédiaire de Didier Lacour qui dispensait des formations sur la cotation fonctionnelle. Il m’avait proposé un stage chez Rolex sur la Conception d’un fermoir de montre avec 2 aspects : la conception et la simulation numérique d’un fermoir. Et j’ai été embauché suite à mon stage dans le même service (Conception Bijouterie) qui recherchait des ingénieurs en simulation numérique, une discipline grandissante chez Rolex.
A quoi ressemble une journée type de travail ?
Élodie : Je travaille sur un projet principal, pour lequel je suis en interaction avec des horlogers, d’autres ingénieurs et des constructeurs. Nous discutons des essais à mener, de la manière de le faire, de l’analyse des résultats, de la gestion des risques... Il faut préparer le travail de l’horloger, assurer la coordination avec les autres ingénieurs, partager ses résultats, mais aussi les synthétiser et en rendre compte. J’ai un rôle d’expertise donc je peux par ailleurs être sollicitée pour apporter un avis sur d’autres projets. Concrètement j’ai beaucoup de réunions, avec beaucoup de gens différents. Je suis aussi en charge de faire évoluer nos méthodes.
Julien : Je vais plutôt présenter une semaine type. Nous travaillons en mode projet donc certaines journées sont réservées pour ces projets où nous travaillons en équipe pluridisciplinaires (Designer, bureau d’étude, méthode, achat, gestion, … pour les projets produit, il y a aussi des personnes des services informatiques et des processus pour les projets comme le PLM). Lors de ces journées, une partie est dédiée aux séances collégiales sur le projet : avancement, planning, remontée des points durs,… le reste permet de travailler avec d’autres membres du projet sur des points particuliers, toute l’équipe étant disponible sur ce créneau.
Nous avons aussi une journée dans la semaine réservée aux partages dans le service pour assurer la coordination des différents projets, apporter un soutien technique aux collègues, chacun ayant son domaine d’expertise, valider et partager les décisions.
En plus de ça, j’ai quelques actions d’administrateur ou de soutien pour le PLM.
Quel est le projet sur lequel vous avez travaillé et dont vous êtes les plus fiers ?
Élodie : Il s’agit du développement d’une famille de calibres. J’ai travaillé plus de 5 ans sur ce projet. Il a abouti et ces calibres équipent aujourd’hui une grosse partie de nos montres. Ce fut un vrai défi à relever compte tenu des enjeux, des délais et du nombre important de parties prenantes.
Julien : La mise en place du PLM pour les données des bureaux d’étude. On a pu revoir complètement l’organisation de nos données, ajouter des outils de recherche et de reporting dédiés à nos activités de bureau d’étude. Il a fallu comprendre les besoins de tous, convaincre des intérêts, superviser les équipes de migrations. Il y avait régulièrement des surprises : les données migrées pouvaient avoir été créées il y a plus de 15 ans avec des versions de logiciel CAO et des méthodologies très disparates. Il fallait trouver des solutions pour ne pas interrompre le travail du service tout en basculant le plus rapidement dans le nouveau système pour éviter de rester dans une situation inconfortable avec 2 modes de travail.
Aujourd’hui, ça fait 3 ans qu’on travaille dans ce nouveau système, les équipes se le sont approprié et en apprécient les bénéfices. La gestion de ces données est bien plus rigoureuse, plus flexible et limite les erreurs plus en amont dans le processus, avant que les pièces soient fabriquées.
Considérez-vous faire un métier d'ingénieur et vous servez vous encore aujourd'hui d'enseignements appris à Centrale Lyon ?
Élodie : Oui aujourd’hui je fais un métier d’ingénieur. On me demande d’analyser, d’anticiper, de synthétiser, de gérer des risques, de travailler en équipe, de faire des choix et des propositions d’évolution. Je me sers encore aujourd’hui de compétences techniques acquises à Centrale (mécanique, matériaux, statistiques, etc), mais je crois que ce que l’Ecole m’a le plus apporté, c’est de savoir apprendre, de savoir synthétiser et avoir une vision globale des problèmes.
Julien : Mon métier est celui d’un ingénieur. Je me sers peu des enseignements techniques appris à l’Ecole, par contre mon parcours à Centrale Lyon m’a appris à analyser des problématiques, à faire des choix, à les justifier, à synthétiser mes réflexions et à aller chercher la connaissance là où elle est et à m’adapter. Je n’ai pas de responsabilité hiérarchique, je dois donc convaincre pour faire passer mes idées.
Qu'est ce qui vous plaît le plus dans vos métiers ?
Élodie : Le fait de travailler sur un beau produit qui est à la fois technique et esthétique, et le faire en équipes de projet pluri-disciplinaires. J’ai beaucoup d’interactions avec plein de gens et de métiers différents !
Julien : J’aime le fait d’avoir des problématiques à résoudre et, j’ai la chance de pouvoir le faire, sur des activités très variées :
- Innovation sur des systèmes novateurs pour lesquels toutes les voies sont possibles
- Problématiques industrielles avec peu de marge de manœuvre
- Optimisation sur des produits série, ou pour le SAV
- Plus les projets métiers comme le PLM avec des problématiques informatiques, organisationnelles
Vous travaillez sur quoi en ce moment ?
Élodie : Sur la fiabilisation d’un nouveau calibre. Je n’en dirai pas plus…
Julien : Le déploiement du PLM pour le SAV, la conception d’une nouvelle montre, et nous avons des réflexions autour du Model-Based Enterprise.
Comment vos métiers ont-ils évolué depuis 15 ans ?
Élodie : Les moyens de tests et d’analyse sont de plus en plus précis, on arrive par exemple maintenant à mesurer des couples de l’ordre du microNewton x mètre ou à observer des phénomènes dynamiques très brefs à l’aide d’une caméra rapide, choses qui étaient impossibles avant. Cela nous permet d’aller plus loin dans la caractérisation de nos calibres et dans la compréhension des phénomènes. On a également beaucoup progressé dans la gestion des risques, en utilisant notamment mieux les statistiques et les retours d’expérience.
Julien : La part du numérique et de la simulation est de plus en plus grande. Lorsque j’ai commencé, chaque concepteur faisait sa conception et ses simulations numériques, maintenant, il y a des équipes dédiées à la simulation qui remplace certains tests sur prototype. Il faut toujours trouver des méthodes de travail qui permettent de réduire les temps de développement tout en conservant la qualité qui fait le renom de la marque.
Le numérique prenant une place de plus en plus grande, il faut acquérir une certaine expertise dans ce domaine pour pouvoir continuer de travailler sans être dépendant de quelqu’un d’autre.
Y a t-il eu des bonds technologiques impactants ?
Élodie : Oui, il y a notamment des nouveaux matériaux qui permettent par exemple de se passer de lubrifiant – chose omniprésente dans un mouvement – ou d’aller toujours vers de plus petits composants. La simulation numérique est également de plus en plus performante et permet de dimensionner au plus juste : certaines mesures de caractérisation ne sont ainsi plus forcément nécessaires.
Julien : De nouvelles techniques de mise en forme ou de nouveaux matériaux ont remis et remettent encore aujourd’hui en question la façon de concevoir un produit. Par exemple l’impression 3D, au départ réservée pour les prototypes, devient un moyen de production à part entière. Il faut réapprendre à concevoir pour cette technologie.
Concernant notre façon de travailler, la numérisation change beaucoup de choses : simulation numérique, rendus réalistes, simulation d’usinage,… On ne se passe pas encore de prototypes physiques mais on peut valider de plus en plus de choses numériquement.
Existe t-il une forme de routine dans vos métiers ? Vos métiers sont-ils voués à évoluer à l'avenir?
Élodie : Il existe une certaine forme de routine liée aux méthodes de tests et d’analyses utilisées. On ne remet pas en question nos méthodes lors de chaque qualification, même si nous les faisons très régulièrement évoluer ! Mais il y a toujours une part d’inattendu dans les résultats… Chaque produit est différent. Un changement même minime peut réserver des surprises, nous travaillons sur du si petit qu’un rien peut influencer la dynamique d’une fonction ou le fonctionnement d’un ressort ! Mon métier évolue et va encore évoluer, la part de la programmation est par exemple de plus en plus importante, que ce soit pour piloter des essais ou les analyser.
Julien : Oui il y a de la routine, on cherche une certaine stabilité sur le produit et sur nos manières de travailler comme pour la plupart des grandes structures. Mais heureusement l’inattendu trouve encore sa place : lorsqu’on développe un nouveau produit, on n’anticipe pas tous les problèmes, il peut y avoir des changements de norme, des changements de planning qui nous imposent de tout revoir. Avec l’informatique il y a toujours des surprises, parfois bonnes, parfois mauvaises. Lorsqu’on a déployé le PLM, on avait essayé d’anticiper au maximum, mais il y a tellement d’interconnexions dans les données et de manière de les exploiter (selon les différents services, chez nos sous-traitants, …) que certaines problématiques sont apparues lors de la mise en production. Quant à mon métier, il est voué à évoluer. Avec l’industrie 4.0, il y aura certainement de nouvelles compétences à acquérir et d’autres qui vont disparaître. On se pose régulièrement la question de la répartition des rôles dans les équipes : est-ce que chacun doit pouvoir tout faire pour être autonome ou est ce qu’il faut se spécialiser ?
Quels profils d'ingénieurs Rolex recherche t-il ?
Élodie : Les profils d’ingénieurs recherchés sont multiples, Rolex est une grande entreprise (nous sommes plus de 5’000 à Genève !) qui regroupe des métiers très variés. On a besoin de gens qualifiés en matériaux, en conception, en informatique, en programmation, en logistique, en finance, etc
Julien : C’est très varié : en R&D on recherche des ingénieurs matériaux, conception, programmeur, dans les services IT des ingénieurs d’application, en Production des profils orientés sur la logistique, sur les process de fabrication…
Aucun commentaire
Vous devez être connecté pour laisser un commentaire. Connectez-vous.